
Process
The main manufacturing process used at Hepworth Composites is hot compression moulding. This is a mass production route for the manufacture of composite components using closed mould technology.
This process uses a hydraulic press capable of applying a pressure of approximately 100 tonnes per square metre. A hardened steel tool designed to produce the finished component shape is located between the press platens. The tool is heated to approx. 130 to 170°C using either heated platens or directly using oil, electric or steam. The composite SMC or DMC mix is then placed in tool and pressure rapidly applied to the moulding compound. After a period of time, dependent on wall thickness, the thermoset cure is completed and the tool is opened and the finished component removed.
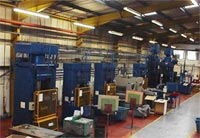
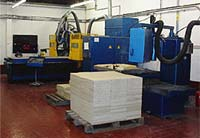
At Hepworth Composites we have a large number of presses and a wide range of platen sizes, up to 4m x 4m, with press tonnage from 150 T to 1500 T.
We also operate a 3 axis CNC routing facility to give consistent finishing of mouldings and drilling of holes and fixing points. There are 3 CNC routing machines to cover a wide range of sizes of mouldings.
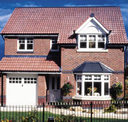
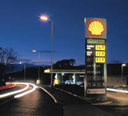
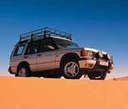